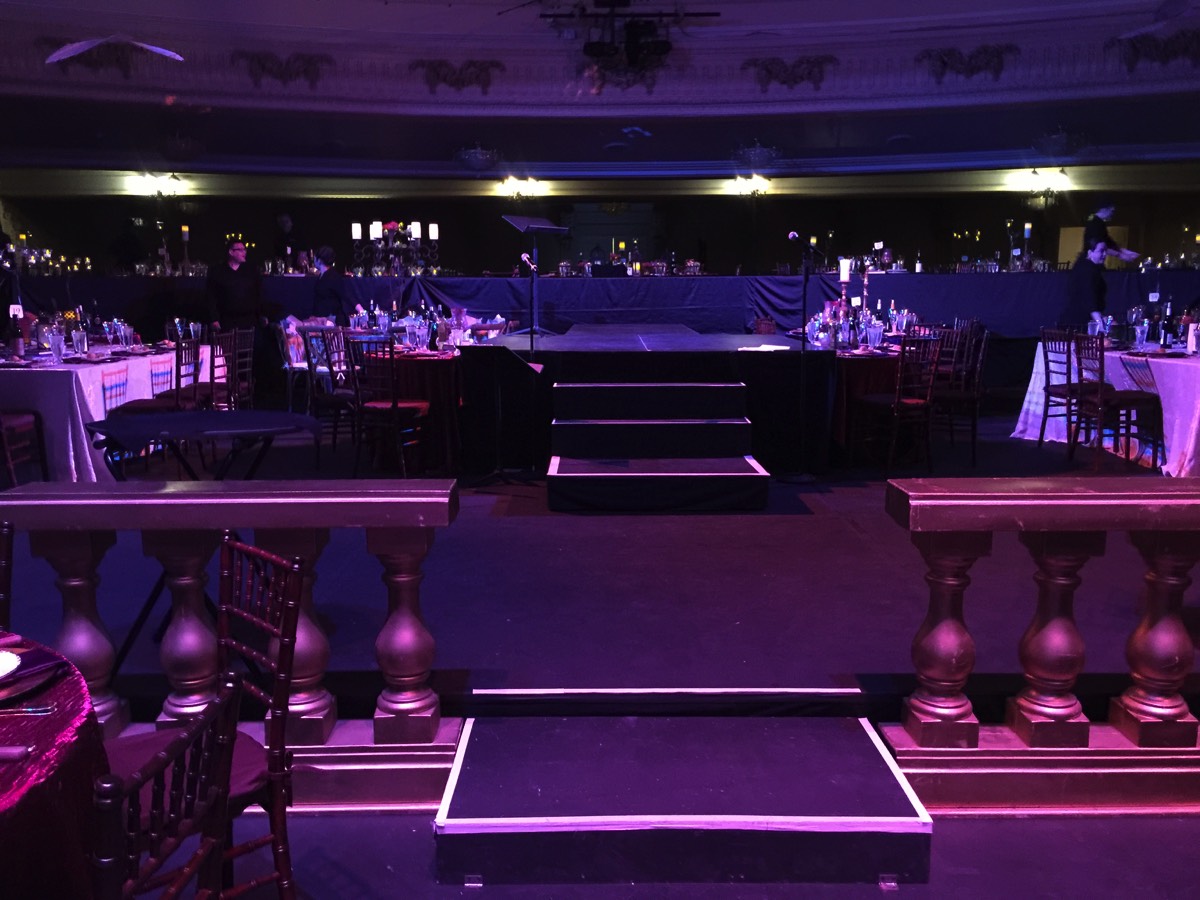
BCPA Star Chefs Custom Stage Project
The Broadway Center for the Performing Arts is a three theatre complex, based in Tacoma Washington. They manage and operate the Pantages Theatre, The Rialto Theatre, and the Theatre on the Square. They have an annual fundraiser called "Star Chefs" which they hold in the Pantages Theatre's auditorium.
For anyone who is familiar with how plated fundraisers usually work, they involve serving dinner at a seated table, which is not usually compatible with a theatre auditorium. Here is what the auditorium looks like, view from the stage:
For anyone who is familiar with how plated fundraisers usually work, they involve serving dinner at a seated table, which is not usually compatible with a theatre auditorium. Here is what the auditorium looks like, view from the stage:
We were asked to create a custom stage extension that would reach most of the way to the theatre's back wall. Here is what we were contracted to do:
• Build custom stage for seating and performance over Pantages Theatre auditorium seats. Graduated stage width 56' wide at existing auditorium stage out to 72' wide at house rear.
• Deck surfaces clean and painted or covered
• Custom Step Units to connect levels
• Handrail along sides, levels and rear
• Ramps from the Pantages House to the rear of the custom extension.
The schedule we had to work from was tight, but doable:
• Proposal submitted by February 3, 2017
• Technical drawings completed by February 15, 2017
• Detail Installation plan Submitted by February 20, 2017
• Installation begins March 19, 2017
• Installation complete by March 21, 2017
• Load-out begins March 29th 2017
Ok, that seems simple enough.
There were two challenges we had to plan for. First, the theatre seating is "raked" which means that the farther towards the back of the seating you go, the higher in elevation the seats are- see image above. Second, the Pantages floor is concave, which means it is higher at the outside edges than the center, and just to complicate matters the seating rows are curved, so the height of the seating rows move in three dimensions. Also, the seating rows and heights are not symmetrical…
Here is the only drawing of the house anyone had, while it is helpful, it doesn't really give us an idea of the heights we had to work with:
• Build custom stage for seating and performance over Pantages Theatre auditorium seats. Graduated stage width 56' wide at existing auditorium stage out to 72' wide at house rear.
• Deck surfaces clean and painted or covered
• Custom Step Units to connect levels
• Handrail along sides, levels and rear
• Ramps from the Pantages House to the rear of the custom extension.
The schedule we had to work from was tight, but doable:
• Proposal submitted by February 3, 2017
• Technical drawings completed by February 15, 2017
• Detail Installation plan Submitted by February 20, 2017
• Installation begins March 19, 2017
• Installation complete by March 21, 2017
• Load-out begins March 29th 2017
Ok, that seems simple enough.
There were two challenges we had to plan for. First, the theatre seating is "raked" which means that the farther towards the back of the seating you go, the higher in elevation the seats are- see image above. Second, the Pantages floor is concave, which means it is higher at the outside edges than the center, and just to complicate matters the seating rows are curved, so the height of the seating rows move in three dimensions. Also, the seating rows and heights are not symmetrical…
Here is the only drawing of the house anyone had, while it is helpful, it doesn't really give us an idea of the heights we had to work with:
The first step was to build a team to advance the project. Our project Lead was Michael Figueroa. He was then paired up with our production Manager Zayne Goering and Shop Manager Brendan Geier
The next thing we needed to do was create technical measurements, so Mike and team went down to the theatre and spent a day measuring everything they could.
One concern we had, was that the chandeliers that hand under the Pantages balcony would be too close and people would bump their heads on them.
We knew that based on technical measurements, we would have to make the stage extension two levels. Each level would be a step up of 24" the first from the Pantages Stage, the second from the extension. That would give us just enough room to walk under the balcony, and clear all the seats.
After we had measurements, we decided to use our Wenger Strata stage system to build on the lower level, and that we would have to fabricate a custom system for the upper level.
Here were our first sets of technical drawings:
The next thing we needed to do was create technical measurements, so Mike and team went down to the theatre and spent a day measuring everything they could.
One concern we had, was that the chandeliers that hand under the Pantages balcony would be too close and people would bump their heads on them.
We knew that based on technical measurements, we would have to make the stage extension two levels. Each level would be a step up of 24" the first from the Pantages Stage, the second from the extension. That would give us just enough room to walk under the balcony, and clear all the seats.
After we had measurements, we decided to use our Wenger Strata stage system to build on the lower level, and that we would have to fabricate a custom system for the upper level.
Here were our first sets of technical drawings:
We went through a few design changes, and decided that the upper level would consist of 44 custom 4' wide by 12' long frames, and six custom size frames, that we would lay standard 4' x 8' stage decks on. The reason behind the 4 x 12 frames, was so we could build custom legs, and minimize the need to remove seats and to accommodate the uneven floor.
In order to accommodate the height of the second level we decided to lower the height of the first level during the installation.
The decision was made to lay the 4x8 decks at a 90 degree orientation to the frames to increase stability.
In order to accommodate the height of the second level we decided to lower the height of the first level during the installation.
The decision was made to lay the 4x8 decks at a 90 degree orientation to the frames to increase stability.
It took about three weeks to get all of the materials and final drawings ready, and manufacturing took approximately seven days. The decision was made to cut all stage legs, cross bracing and handrail on site to make sure all measurements were perfect and to minimize having to remove seats and rebuild in case we ran into any architectural obstacles.
We started building onsite March 19, 2017 and completed the deck build in three days (right on the schedule). We needed two additional ½ days onsite to complete the ramps and handrail. The handrail was custom cut using aluminum pipe and speed rail fittings.
We made 296 legs and sixteen custom handrail pieces.
The biggest obstacle our team encountered was that handrail and ramps were too close to existing architecture, so on the ground custom solutions were needed. We cleared the built in chandeliers with plenty of room to spare.
Of course, we had a day of creating final as built drawings and a full label system for the legs and frames so we can reinstall the system again.
Here are some pictures of the project:
We started building onsite March 19, 2017 and completed the deck build in three days (right on the schedule). We needed two additional ½ days onsite to complete the ramps and handrail. The handrail was custom cut using aluminum pipe and speed rail fittings.
We made 296 legs and sixteen custom handrail pieces.
The biggest obstacle our team encountered was that handrail and ramps were too close to existing architecture, so on the ground custom solutions were needed. We cleared the built in chandeliers with plenty of room to spare.
Of course, we had a day of creating final as built drawings and a full label system for the legs and frames so we can reinstall the system again.
Here are some pictures of the project:
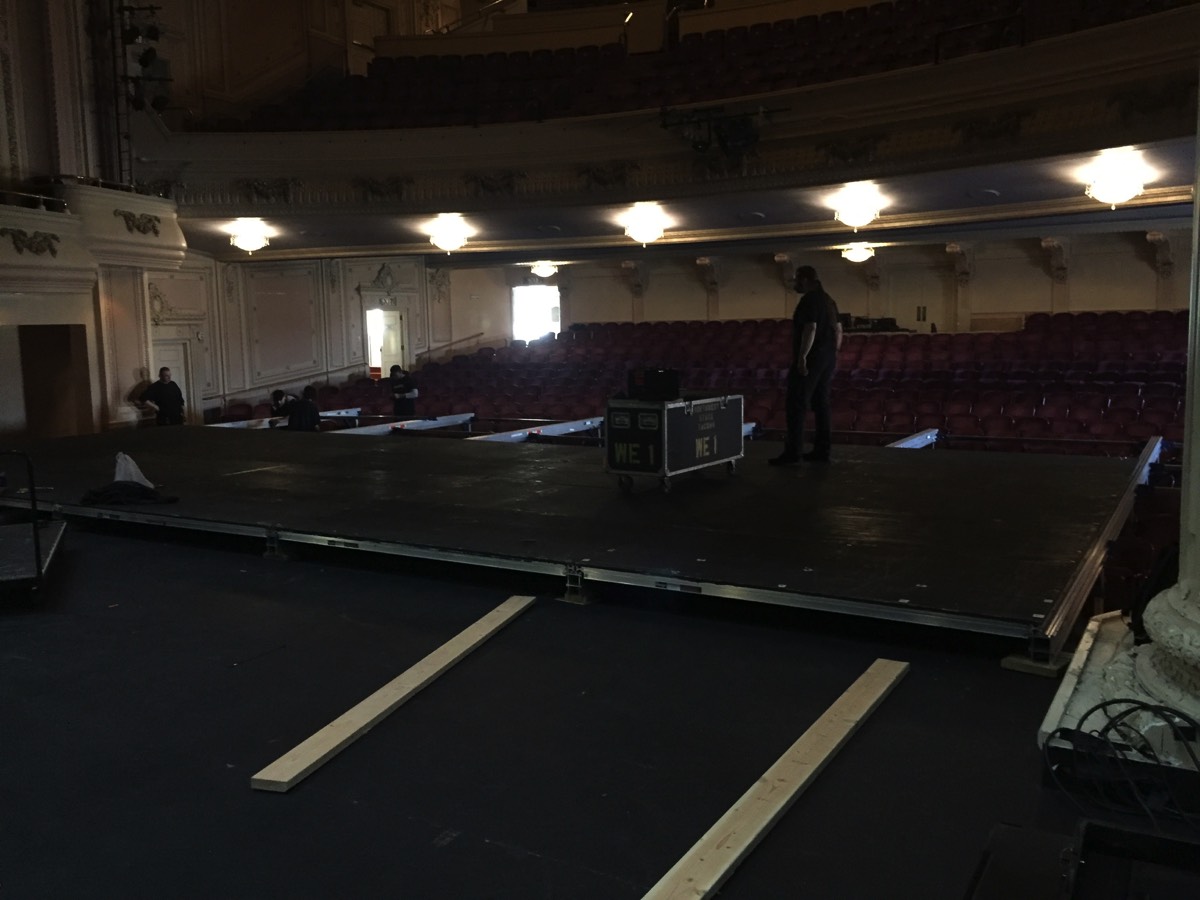
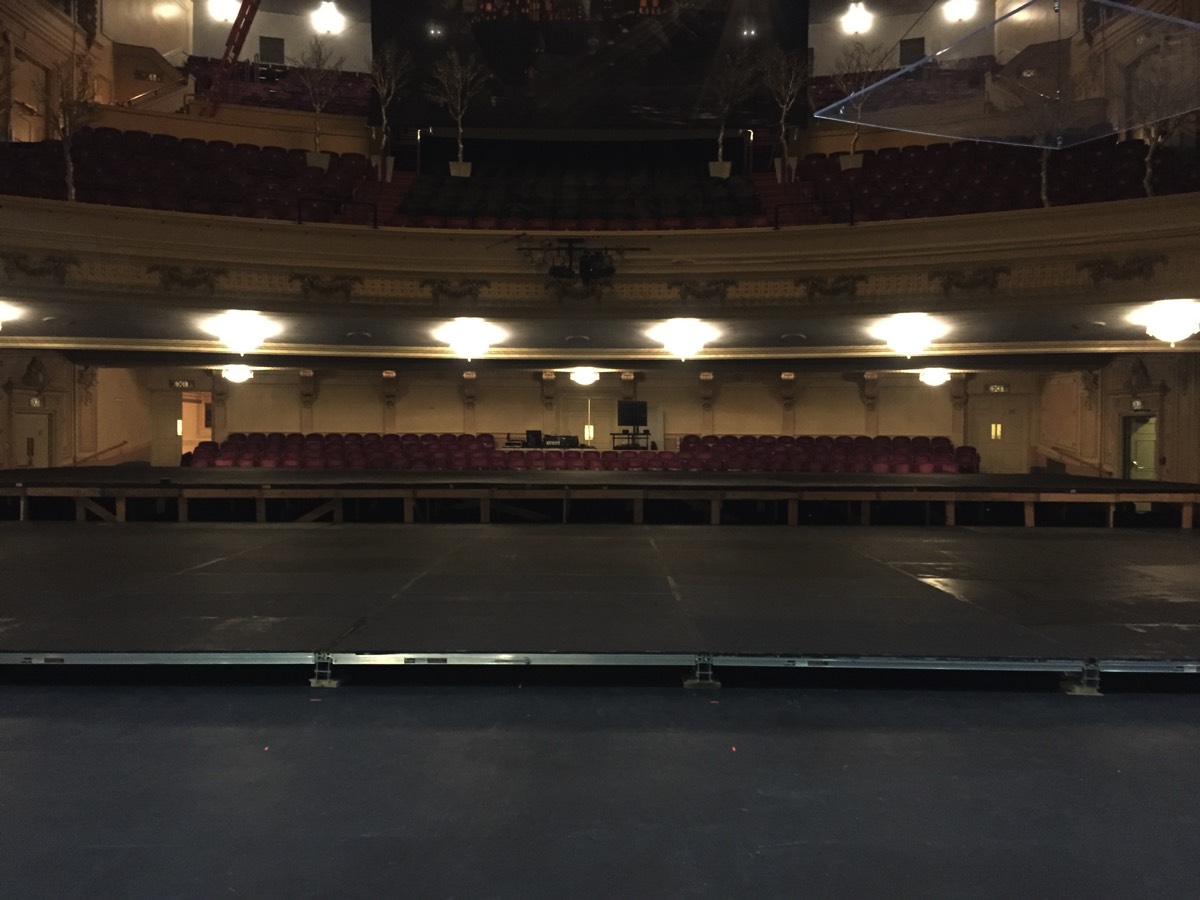
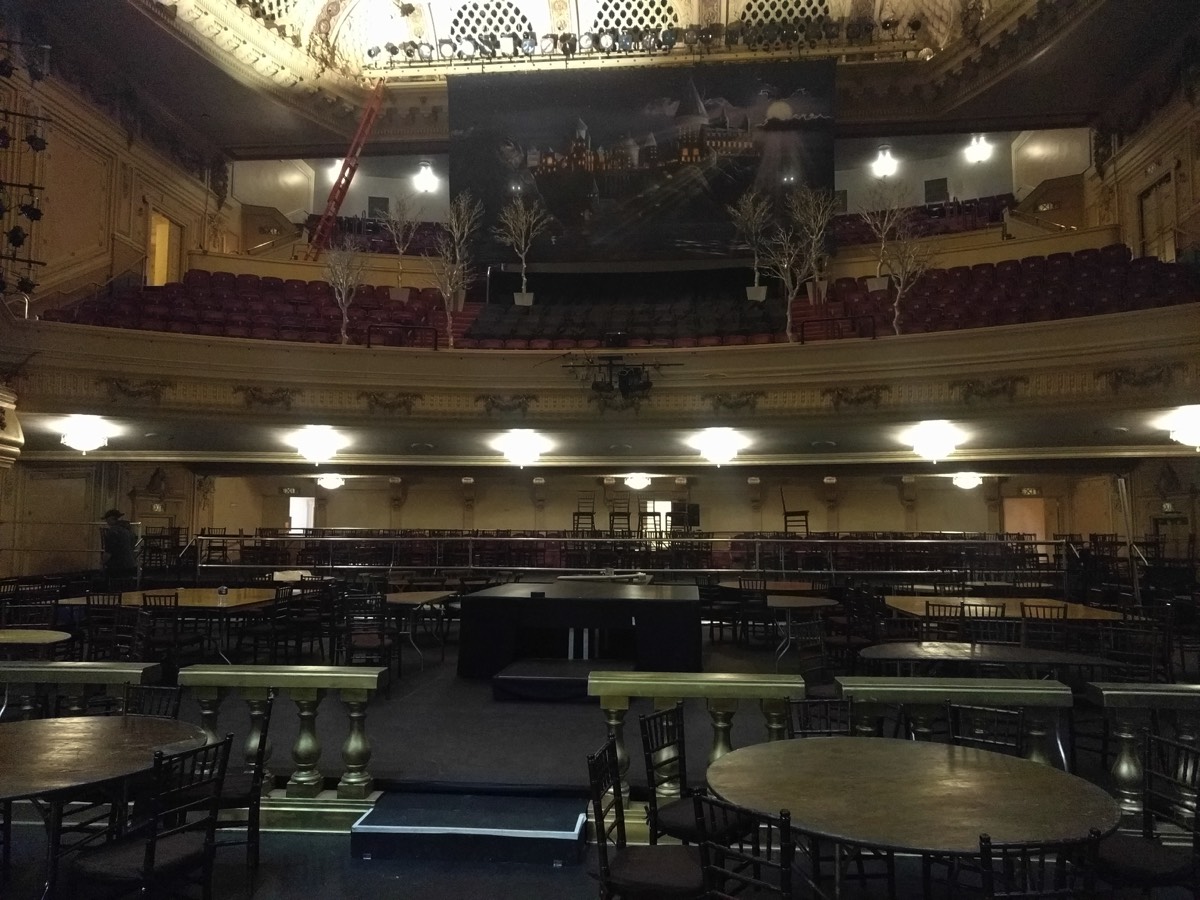
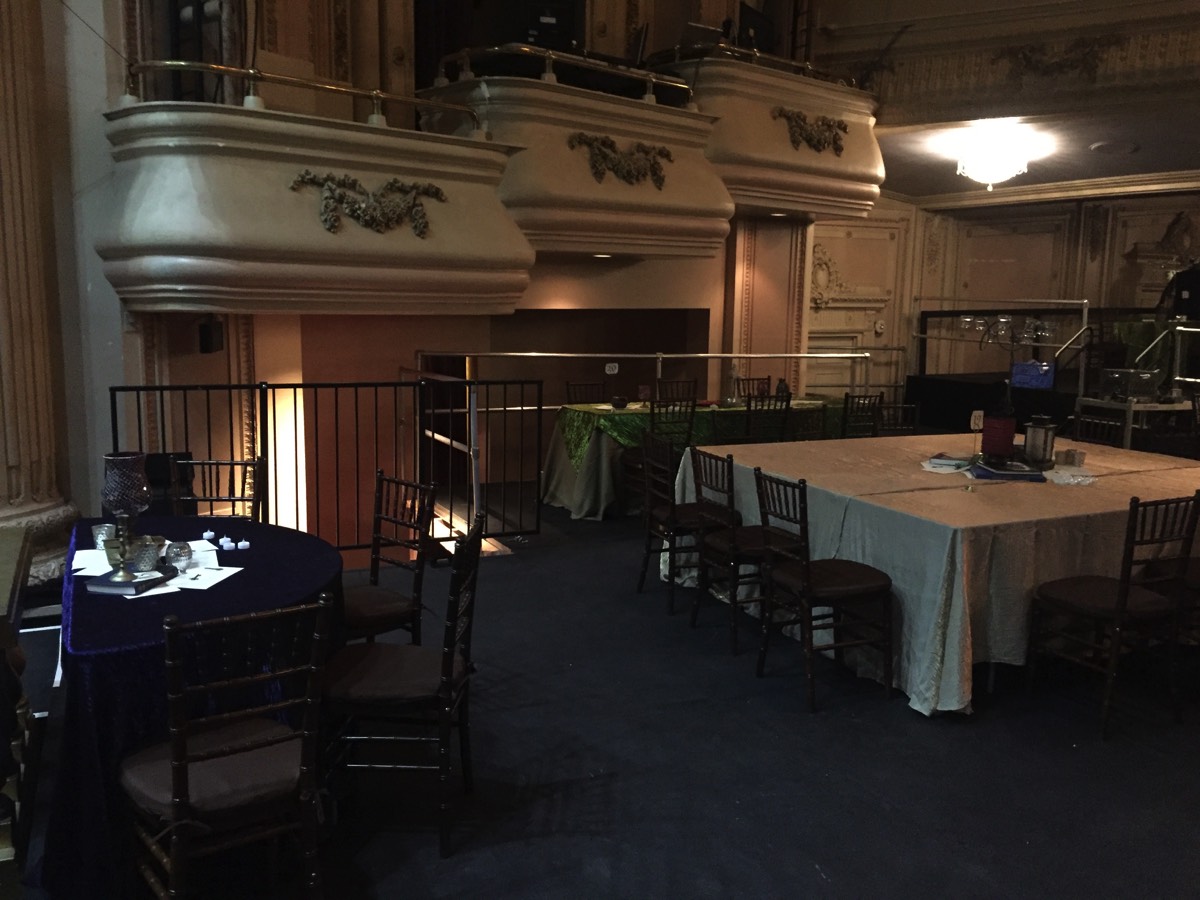
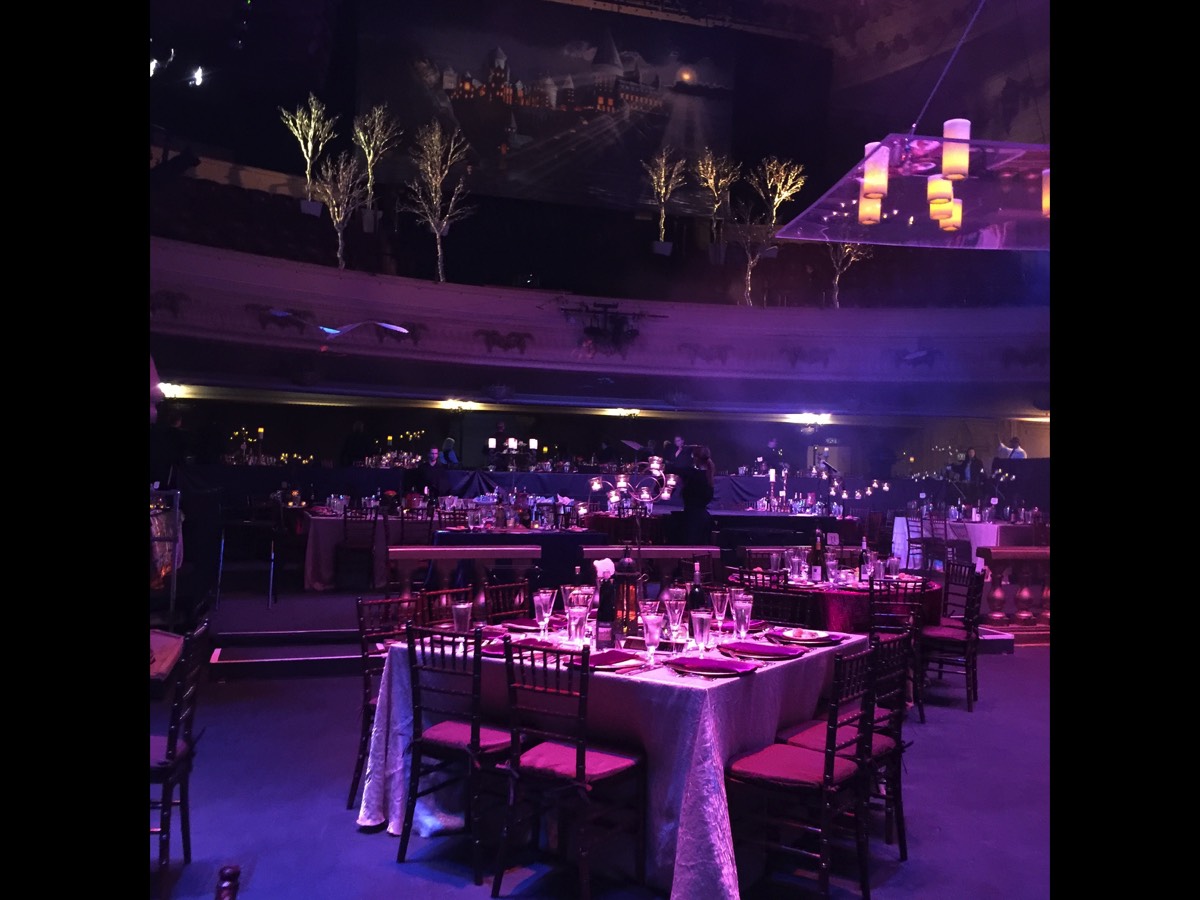
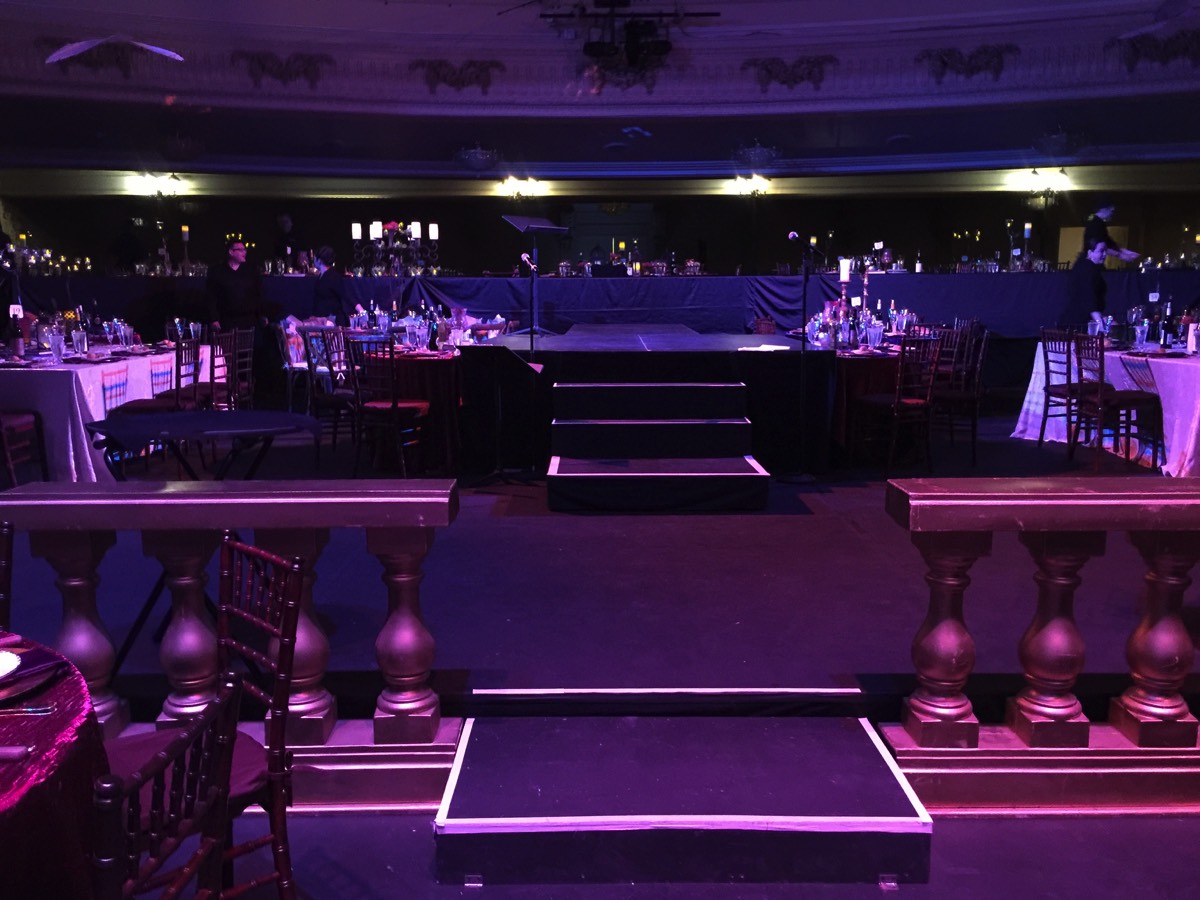
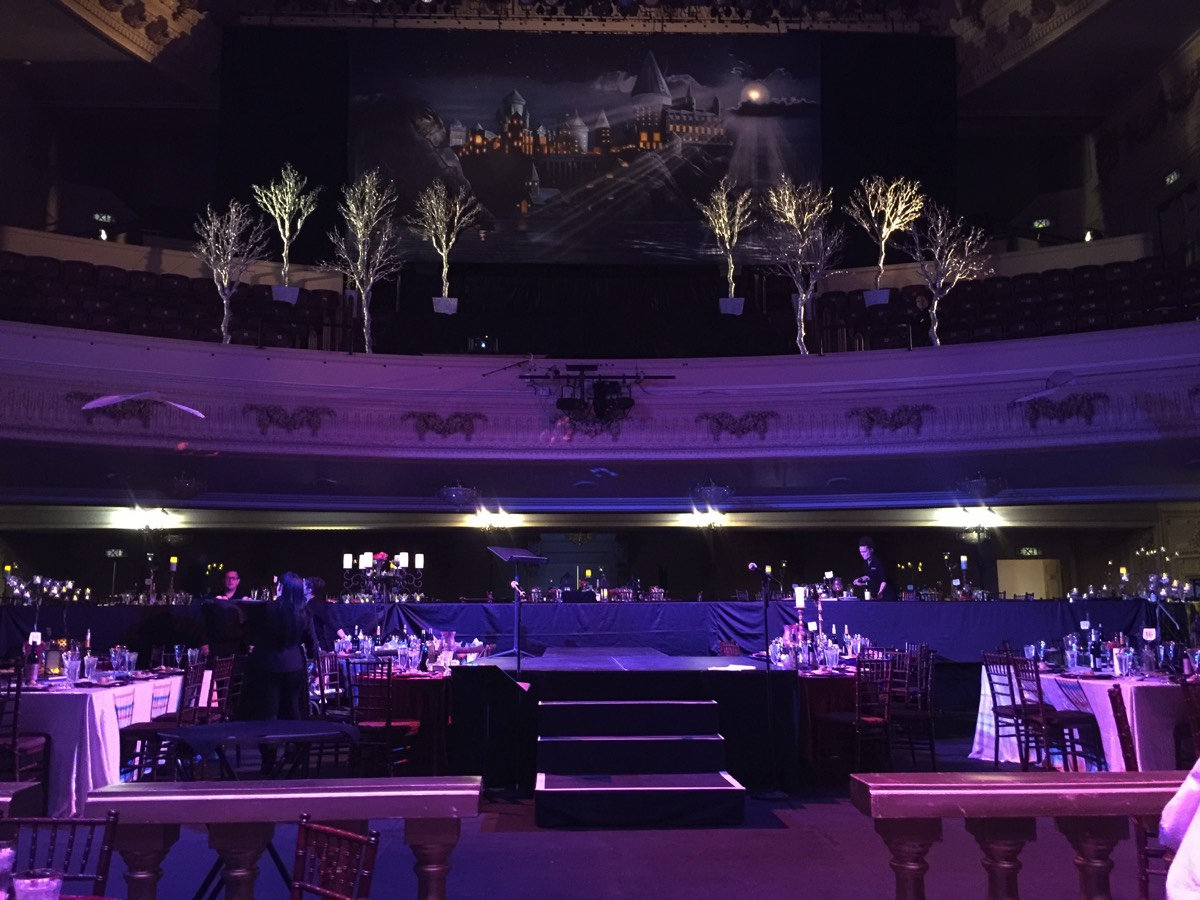

~r